Bank 1 air-fuel ratio imbalance – a common issue causing dodgy engine performance. This ain’t no minor glitch, it’s a serious problem that can lead to major engine woes if left unaddressed. Think misfires, rough idling, and potentially damaged components. Understanding the root cause and fixing it properly is key to keeping your ride running smoothly.
This guide breaks down the issue, from diagnosing the problem to sorting out the repairs and preventing future issues. We’ll cover everything from fuel delivery systems to ignition problems, plus a visual breakdown to help you picture the issue.
Defining Air-Fuel Ratio Imbalance in Bank 1
An air-fuel ratio imbalance in a specific engine bank, such as bank 1, signifies a deviation from the stoichiometric ratio of air to fuel required for optimal combustion. This disparity in the fuel-air mixture can lead to significant performance issues and potential engine damage if not promptly addressed. Understanding the causes, symptoms, and diagnostic methods is crucial for maintaining engine health and efficiency.Air-fuel ratio imbalance in bank 1, a critical parameter in internal combustion engines, arises when the fuel and air mixture entering the cylinders of that bank are not perfectly balanced.
This imbalance disrupts the combustion process, resulting in variations in power output, emissions, and potentially harmful consequences for engine components. Such imbalance often manifests in measurable discrepancies in exhaust gas composition and engine performance, demanding prompt attention.
Symptoms of Air-Fuel Ratio Imbalance in Bank 1
Variations in engine performance are a primary symptom of air-fuel ratio imbalance in bank 1. These variations may include fluctuations in engine speed, power output, and overall smoothness. Drivers may notice an erratic acceleration response, rough idling, or a significant decrease in engine power. Further indicators include noticeable changes in exhaust emissions, such as an increase in exhaust smoke, a different exhaust odor, or a noticeable change in exhaust gas temperature.
Additionally, warning lights on the dashboard might illuminate, signaling a potential problem.
Underlying Mechanisms of Air-Fuel Ratio Imbalance in Bank 1
Several factors can contribute to air-fuel ratio imbalances in bank 1. Malfunctioning or improperly calibrated fuel injectors are a frequent culprit, causing inconsistent fuel delivery to the cylinders in the affected bank. Issues with the intake manifold, such as leaks or blockages, can alter the air flow, leading to an imbalanced fuel-air mixture. Similarly, problems with the engine’s sensors or the electronic control unit (ECU) responsible for managing the air-fuel ratio can create the imbalance.
Yo, Bank 1 air-fuel ratio imbalance is kinda a big deal, right? Like, totally messing up your engine. But hey, when you’re tryna chill after a long day fixing that, checking out some pizza spots in Port Aransas is a total vibe. Pizza places in Port Aransas are totally fire, you know? Gotta get that fuel sorted out though, back to fixing that Bank 1 issue ASAP.
Problems with the intake manifold’s geometry, for example, might lead to uneven air distribution. Additionally, a malfunctioning throttle position sensor can influence the ECU’s calculations, leading to a mismatched air-fuel ratio.
Sensor Types for Air-Fuel Ratio Monitoring in Internal Combustion Engines
Various sensor types monitor the air-fuel ratio in internal combustion engines. These sensors provide real-time data to the engine’s control unit, which then adjusts the fuel injection accordingly.
- Oxygen Sensors (Lambda Sensors): These sensors are crucial for monitoring the oxygen content in the exhaust gases. They measure the difference in oxygen levels between the exhaust gases and the theoretical air-fuel mixture, signaling imbalances to the ECU. Oxygen sensors are typically positioned in the exhaust manifold, downstream of the catalytic converter, allowing them to assess the oxygen content in the exhaust gases.
They are critical in ensuring the efficient combustion of the fuel and minimizing harmful emissions. Their precise placement within the exhaust system is critical for accurate readings, and variations can impact the accuracy of the air-fuel ratio measurements.
- Mass Airflow (MAF) Sensors: MAF sensors measure the mass flow rate of air entering the engine. This data is essential for calculating the air-fuel ratio. MAF sensors are usually positioned in the intake air duct, often close to the throttle body. These sensors are sensitive to changes in ambient conditions, which can impact their accuracy. Precise positioning and calibration are paramount for accurate measurements, and damage to the MAF sensor can lead to significant air-fuel ratio imbalances.
- Fuel Pressure Sensors: Fuel pressure sensors monitor the fuel pressure within the fuel system. Variations in fuel pressure can lead to inaccurate fuel delivery, affecting the air-fuel ratio. These sensors are usually located within the fuel rail or pump assembly. Regular monitoring of fuel pressure is essential to detect any discrepancies that might affect the air-fuel ratio, potentially leading to miscalculations and subsequent issues.
Causes of Bank 1 Air-Fuel Ratio Imbalance
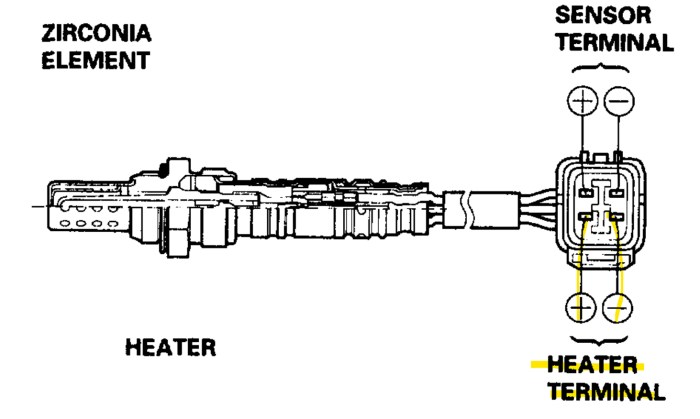
A critical aspect of engine performance lies in maintaining a precise air-fuel ratio within each cylinder bank. Disruptions in this balance, particularly in Bank 1, can manifest as reduced power output, increased emissions, and potentially, engine damage. Understanding the potential causes of this imbalance is essential for effective diagnosis and repair.Fuel delivery issues within Bank 1 can significantly impact the air-fuel ratio.
Problems with the injectors, fuel pumps, or fuel lines can lead to inconsistent fuel delivery to the cylinders, resulting in an uneven mixture. This unevenness directly translates to a bank 1 air-fuel ratio imbalance. Furthermore, issues with the fuel pressure regulator can also contribute to this problem by not maintaining consistent pressure across all injectors in bank 1.
Fuel Delivery System Issues in Bank 1
Fuel delivery systems are intricate networks of components that must function in concert to provide the correct fuel volume to each cylinder. Malfunctioning fuel injectors, a common culprit, can lead to an incomplete or excessive fuel delivery in one or more cylinders of Bank 1. Clogged fuel filters or restricted fuel lines hinder proper fuel flow, potentially creating a significant air-fuel ratio imbalance in Bank 1.
Faulty fuel pumps, whether delivering insufficient or inconsistent pressure, can also cause this issue. The fuel pressure regulator’s role in maintaining a constant fuel pressure is crucial. A malfunctioning regulator can lead to a difference in fuel pressure across the injectors in bank 1, directly affecting the air-fuel ratio.
Intake Manifold and Air Intake System Issues in Bank 1
The intake manifold and air intake system are critical for delivering the correct amount of air to each cylinder. Leaks or restrictions in the intake manifold can alter the air flow to individual cylinders in bank 1, affecting the air-fuel ratio. A clogged air filter, a restricted intake duct, or a damaged intake manifold gasket can all cause uneven air delivery, creating a bank 1 air-fuel ratio imbalance.
The intake manifold design itself, if not properly configured for the specific engine’s needs, can contribute to an uneven air flow distribution. For example, a manifold that restricts airflow to certain cylinders will result in a leaner air-fuel mixture in those cylinders and a richer mixture in others.
Ignition System Component Problems in Bank 1, Bank 1 air-fuel ratio imbalance
Ignition system components are vital for proper combustion. Misfiring spark plugs in bank 1 can lead to incomplete combustion, which will affect the air-fuel ratio in the respective cylinders. Problems with the ignition coils or the distributor (if applicable) can similarly cause misfires, resulting in an imbalance in the air-fuel ratio. Damaged or worn spark plug wires can also lead to irregular firing patterns in Bank 1, contributing to an imbalance.
Sensor and Connection Issues in Bank 1
Engine sensors, particularly the oxygen sensors and mass airflow sensors, are crucial for monitoring and adjusting the air-fuel ratio. Faulty sensors can provide inaccurate readings to the engine control unit (ECU), leading to incorrect adjustments in fuel delivery. Loose or corroded sensor connections can also disrupt the signal transmission, leading to a bank 1 air-fuel ratio imbalance. A damaged or faulty lambda sensor, for example, can provide inaccurate feedback on the exhaust gas composition, leading to incorrect fuel trim adjustments by the ECU.
Comparison of Bank 1 Air-Fuel Ratio Imbalance Causes
Cause | Impact | Typical Symptoms |
---|---|---|
Fuel injector malfunction | Inconsistent fuel delivery to specific cylinders | Reduced power, rough idling, misfires, hesitation |
Clogged fuel filter | Restricted fuel flow | Reduced power, hesitation, rough idling, potentially stalling |
Intake manifold leak | Uneven air flow distribution | Reduced power, rough idling, inconsistent acceleration, potentially misfires |
Clogged air filter | Restricted airflow to specific cylinders | Reduced power, hesitation, rough idling, potentially misfires |
Misfiring spark plug | Incomplete combustion | Reduced power, rough idling, misfires, hesitation, potential engine damage |
Faulty oxygen sensor | Incorrect air-fuel ratio adjustments | Reduced power, rough idling, erratic performance |
Diagnosing Bank 1 Air-Fuel Ratio Imbalance
Diagnosing an air-fuel ratio (AFR) imbalance in bank 1 of an engine requires a systematic approach, combining theoretical understanding with practical diagnostic tools. The imbalance often manifests as performance issues, increased emissions, or even engine damage if left unaddressed. Identifying the root cause necessitates a methodical process that considers various potential factors, including sensor malfunctions, actuator problems, and even issues within the engine’s intake or exhaust systems.A thorough diagnosis begins with a comprehensive understanding of the expected AFR range for the specific engine and operating conditions.
This understanding forms the basis for evaluating any deviations from the norm. Critical to the process is the recognition that an AFR imbalance in bank 1 often correlates with a malfunction in one or more components related to that bank. This understanding allows for a focused and efficient diagnostic procedure.
Systematic Diagnostic Procedure
A systematic diagnostic procedure for an AFR imbalance in bank 1 involves several key steps. First, a visual inspection of the components within bank 1, including fuel injectors, intake manifolds, and exhaust components, should be conducted to identify any obvious signs of damage or blockage. Second, the engine’s operating parameters should be carefully monitored. This includes checking for abnormal sounds, unusual vibrations, and significant changes in engine performance.
Third, the diagnostic tools are used to collect data on the actual AFR. The readings are crucial in determining if the imbalance exists and the severity of the issue.
Role of Diagnostic Tools and Equipment
Diagnostic tools and equipment play a vital role in identifying the root cause of an AFR imbalance in bank 1. Sophisticated engine analyzers, often integrated with onboard diagnostic (OBD) systems, can provide real-time data on various engine parameters, including AFR. These tools offer valuable insights into the engine’s operational status, including readings from the oxygen sensors and other relevant components.
Oscilloscope readings, for example, can highlight fluctuating readings, indicating potential issues with sensor signals. Moreover, specialized diagnostic software can interpret and analyze the data from these tools, revealing trends and anomalies that may be indicative of specific problems.
Testing Air-Fuel Ratio Sensors and Actuators
Testing air-fuel ratio sensors and actuators is a crucial step in the diagnosis. Air-fuel ratio sensors are often tested by applying a known air-fuel mixture to the sensor and observing the output signal. Actuators, such as fuel injectors, can be checked using a diagnostic tool to verify their operation. This involves observing the injector’s electrical pulse and comparing it to the expected pattern.
Discrepancies from expected values can pinpoint problems within the actuators or the system controlling them. A significant variation in injector pulse width, for instance, might indicate a malfunction in the fuel pump or the ECU.
Comparing Sensor Readings Between Banks
Comparing sensor readings from bank 1 with those from the opposite bank (bank 2) is essential for pinpointing the imbalance. A consistent difference in AFR between the two banks strongly suggests a problem localized to bank 1. For example, if bank 1 consistently shows a lean condition while bank 2 is within the normal range, this strongly indicates a problem within bank 1.
Such comparisons provide a baseline for determining whether the issue is specific to one bank or systemic.
Potential Problems with Bank 1 Sensors and Symptoms
- Oxygen Sensor Malfunction: A faulty oxygen sensor in bank 1 may produce erratic or inconsistent readings, leading to a fluctuating AFR. This often results in poor engine performance, especially under varying loads. The engine may also experience a hesitation or rough idle.
- Fuel Injector Malfunction: A malfunctioning fuel injector in bank 1 can deliver inconsistent amounts of fuel, leading to an air-fuel imbalance. This could cause a significant decrease in power output or cause the engine to run poorly, with a noticeable difference in the operation of bank 1 compared to bank 2.
- Intake Manifold Leaks: Leaks in the intake manifold of bank 1 can disrupt the air-fuel mixture, causing a lean condition. This can be detected by a noticeable reduction in power output, especially under acceleration. A hissing sound from the intake manifold might be heard.
- Mass Air Flow Sensor (MAF) Issues: A faulty MAF sensor, if present, may provide inaccurate readings, affecting the air-fuel ratio calculations. Symptoms could include poor acceleration, a rough idle, or intermittent engine misfires, particularly noticeable in bank 1.
Repairing Bank 1 Air-Fuel Ratio Imbalance
Addressing an air-fuel ratio imbalance in Bank 1 necessitates a systematic approach, targeting specific components. Failure to identify and rectify the root cause can lead to diminished engine performance, increased fuel consumption, and potentially, significant engine damage. This section provides a detailed guide to repairing the issue, emphasizing the importance of accurate diagnosis and precise repair procedures.Repairing this imbalance often involves a multifaceted approach, ranging from inspecting and potentially replacing fuel injectors and air intake components to troubleshooting ignition systems and sensors.
Thoroughness is critical to ensure a lasting resolution and prevent recurring problems. A systematic approach, combined with a keen understanding of the vehicle’s specific system, is paramount for successful repair.
Yo, bank 1 air-fuel ratio imbalance is a real problem, right? It’s like, your engine’s not getting the right mix of air and fuel. But hey, you know what can help with that? Checking out the advance puppy food feeding guide might actually give you some insights into balancing things out. It’s all about finding the right ratios, you know?
So, yeah, back to the engine problem, fixing that bank 1 air-fuel ratio imbalance is key for a smooth ride.
Repairing Fuel Injectors in Bank 1
Fuel injectors are crucial for precise fuel delivery. Malfunctioning injectors can disrupt the air-fuel ratio, leading to an imbalance. A systematic approach to fuel injector repair is essential. First, disconnect the negative battery terminal to prevent electrical hazards. Then, carefully remove the injector harness and the injector itself, adhering to the manufacturer’s specifications for torque and procedures.
Visually inspect the injector for damage, such as cracks or blockages. If damage is found, replace the injector with a new, genuine part. After installation, reconnect the injector harness and battery terminal. Testing the system is crucial; verify proper functionality by monitoring the air-fuel ratio using a diagnostic tool.
Repairing or Replacing Faulty Air Intake Components
Air intake components, including the air filter, intake manifold, and hoses, play a critical role in maintaining proper airflow to the engine. Obstructions or leaks in these components can significantly impact the air-fuel ratio. Inspect the air filter for obstructions and replace it if necessary. Carefully examine the intake manifold for cracks or leaks, replacing any damaged sections.
Visually inspect all intake hoses for damage or leaks. Using a pressure gauge can pinpoint leaks in the intake system. Replacing faulty components ensures a smooth and consistent airflow, restoring the proper air-fuel ratio.
Diagnosing and Repairing Ignition System Issues
The ignition system is critical for proper combustion. Malfunctions can lead to a misfire and affect the air-fuel ratio. First, inspect the spark plugs for damage, and replace them if needed. Next, evaluate the spark plug wires for cracks or deterioration. Check the ignition coils and related components for any signs of damage or malfunction.
A no-spark condition can indicate a problem with the ignition control module. Replacing faulty ignition components, including the ignition control module, ensures consistent ignition, contributing to the proper air-fuel ratio.
Troubleshooting Sensor Issues in Bank 1
Sensors provide critical feedback on engine conditions, including the air-fuel ratio. Malfunctioning sensors can lead to an imbalance. A diagnostic tool should be used to pinpoint the specific sensor causing the issue. Potential sensors include the oxygen sensor (O2 sensor), mass airflow sensor (MAF sensor), and throttle position sensor (TPS). Once identified, the faulty sensor should be replaced with a new, genuine part.
Thorough testing is vital; verify that the replacement sensor operates correctly by using a diagnostic tool to monitor the air-fuel ratio.
Typical Repair Costs
Component | Estimated Repair Cost (USD) |
---|---|
Fuel Injector (per injector) | 100-250 |
Air Filter | 25-75 |
Intake Manifold | 200-500 |
Intake Hoses | 50-150 |
Spark Plugs (set) | 50-100 |
Spark Plug Wires (set) | 75-150 |
Ignition Coils (per coil) | 75-200 |
Oxygen Sensor | 50-150 |
Mass Airflow Sensor | 100-300 |
Throttle Position Sensor | 75-200 |
Note: Costs vary based on vehicle make and model, labor rates, and specific parts required. This table provides a general estimate.
Preventing Bank 1 Air-Fuel Ratio Imbalance
Proactive maintenance is crucial in preventing future air-fuel ratio imbalances in Bank 1. Ignoring potential issues can lead to decreased engine performance, increased fuel consumption, and potentially more significant damage. By implementing preventative strategies, owners can extend the lifespan of their engines and avoid costly repairs.Addressing potential issues early through proactive maintenance strategies is key to preventing costly repairs.
This involves understanding the interconnectedness of various components and the subtle warning signs that can precede a more significant problem. Early intervention often results in simpler, less expensive solutions.
Fuel Injector Maintenance in Bank 1
Proper fuel injector maintenance in Bank 1 is paramount. Regular cleaning and inspection can significantly reduce the likelihood of clogging and irregular fuel delivery. This can be achieved through scheduled professional cleaning or DIY methods, utilizing appropriate cleaning solutions. Fuel injector cleanliness directly impacts the precise mixture of fuel and air, crucial for maintaining a balanced air-fuel ratio.
Clogged or malfunctioning injectors can lead to a lean or rich condition, disrupting the optimal balance. Maintaining injector pressure within the manufacturer’s specifications also contributes to reliable fuel delivery.
Maintaining Air Intake Components in Bank 1
Regular inspection and cleaning of air intake components in Bank 1 are vital for preventing imbalances. This includes filters, tubes, and any other components within the intake system. Clogged air filters restrict airflow, impacting the engine’s ability to properly mix fuel and air. Regular replacement of air filters, as recommended by the vehicle manufacturer, is crucial for maintaining consistent airflow.
Furthermore, examining the condition of intake tubes and hoses for leaks or damage is essential. Leaks can compromise the air intake system’s integrity, resulting in an uneven air-fuel mixture. Visual inspections for damage or debris accumulation should be performed regularly.
Ignition System Inspections in Bank 1
Regular ignition system inspections are critical in maintaining optimal performance and preventing issues in Bank 1. Inspecting spark plug condition and ensuring consistent spark output are vital steps. Damaged or fouled spark plugs can lead to an uneven combustion process, directly affecting the air-fuel ratio. Misfires, a common indicator of ignition system problems, can cause lean or rich conditions.
Checking the spark plug gap and the health of the ignition coils are vital parts of a comprehensive inspection. If irregularities are detected, prompt repairs are essential to prevent more significant issues.
Sensor Monitoring and Calibration for Bank 1
Regularly checking and calibrating sensors related to Bank 1 is critical for early detection of potential issues. Sensors such as oxygen sensors, air flow meters, and mass air flow sensors are crucial for the engine’s computer to accurately adjust the air-fuel ratio. Malfunctioning or miscalibrated sensors can result in inaccurate readings, leading to an imbalance. Regular sensor checks are essential for preventing this issue, with scheduled inspections or alerts based on mileage or time recommended by the manufacturer.
Consistent sensor readings are essential for the engine control module (ECM) to maintain the precise balance of fuel and air.
Preventative Maintenance Checklist for Bank 1 Air-Fuel Ratio
- Inspect and clean fuel injectors at recommended intervals.
- Replace air filters per manufacturer guidelines.
- Visually inspect air intake components for leaks or damage.
- Regularly inspect spark plugs for damage or fouling, checking spark plug gap.
- Monitor and calibrate oxygen sensors, air flow meters, and mass air flow sensors at specified intervals.
- Check for leaks and damage in the exhaust system, which can also affect air-fuel ratio.
Illustration of Bank 1 Air-Fuel Ratio Imbalance
Engine air-fuel ratio imbalance in Bank 1 signifies a deviation from the stoichiometric ratio within that cylinder bank. This discrepancy can stem from a multitude of interconnected issues, impacting engine performance, emissions, and potentially causing damage. Understanding the manifestation of this imbalance through visual representations of the affected components and sensor readings is crucial for accurate diagnosis and effective repair.
Detailed Illustration of an Affected Engine
A bank 1 air-fuel ratio imbalance manifests as a discernible difference in combustion efficiency and emissions between the cylinders in that bank. Visual inspection of the exhaust from each cylinder reveals potential variances in color and opacity. Cylinders exhibiting lean conditions (too much air, insufficient fuel) might produce a more whitish or transparent exhaust, whereas cylinders experiencing rich conditions (too much fuel, insufficient air) could display a darker, smoky exhaust.
This visual observation is a preliminary indicator of the problem.
Sensor Readings in Bank 1
Sensor readings provide quantitative data reflecting the air-fuel ratio imbalance. A typical example involves the oxygen sensor readings, which measure the amount of oxygen in the exhaust gases. In a balanced system, the oxygen sensor readings oscillate around a target value, indicating the close-to-stoichiometric air-fuel ratio. In an imbalance, the readings exhibit a persistent deviation in one or more cylinders of Bank 1.
The sensor readings would show a significantly higher or lower value than the target range in the affected cylinders compared to the balanced cylinders in the same bank. A fluctuating or erratic reading further indicates a potential problem in the sensor or related circuitry.
Schematic of the Fuel Delivery System in Bank 1
The fuel delivery system, critical for maintaining the precise air-fuel ratio, comprises various interconnected components. A schematic diagram illustrating the fuel injectors, fuel rail, fuel pump, and related lines is essential for identifying potential obstructions, leaks, or malfunctions. A malfunctioning fuel injector in one cylinder of Bank 1 might lead to an imbalanced air-fuel ratio. Similarly, a restricted fuel line could impede the proper fuel flow to that cylinder.
Inspecting the fuel pressure in the fuel rail for consistency is also important.
Example Schematic Diagram: (Illustrative, not to scale)
[Insert a diagram here showing the fuel rail, injectors, fuel pump, fuel lines for Bank 1]
The diagram would clearly label each component and highlight the crucial connections for proper fuel delivery.
Ignition System in Bank 1
The ignition system plays a crucial role in the combustion process. A spark plug malfunctioning in one cylinder can lead to incomplete combustion and result in a lean air-fuel mixture. A defective ignition coil or a misfiring coil pack in one cylinder can also contribute to the imbalance. Potential failure points include spark plug wear, faulty ignition coils, and misfiring coils, each impacting the air-fuel ratio in the corresponding cylinder.
Numerical Example of Bank 1 Air-Fuel Ratio Imbalance
A real-world scenario could involve oxygen sensor readings (Lambda) in Bank 1:
Cylinder | Lambda Reading |
---|---|
Cylinder 1 | 0.95 |
Cylinder 2 | 0.95 |
Cylinder 3 | 0.40 |
Cylinder 4 | 0.95 |
In this example, Cylinder 3 shows a significantly lower Lambda reading, indicating a rich condition. This disparity in the sensor readings across the cylinders in Bank 1 points to an air-fuel ratio imbalance. Further investigation would be necessary to pinpoint the precise cause, such as a clogged injector or a problem in the ignition system. These are just illustrative values; actual readings depend on the specific engine and its operating conditions.
End of Discussion
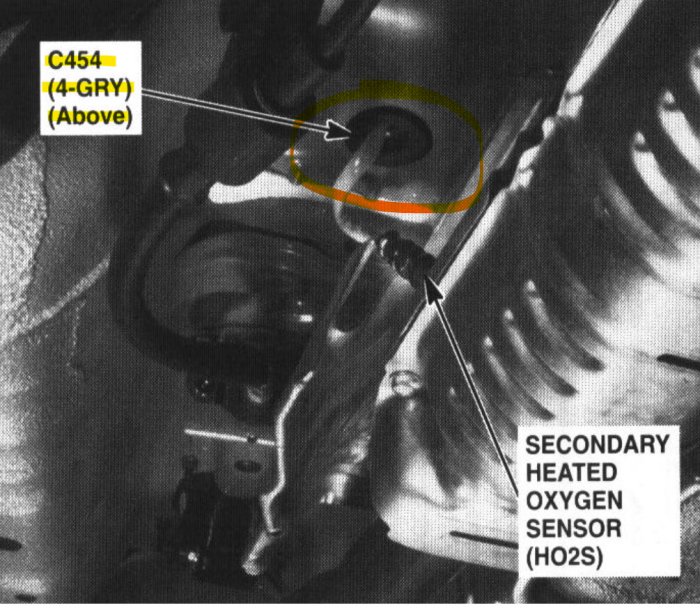
So, bank 1 air-fuel ratio imbalance isn’t rocket science, but it does need attention. This guide has equipped you with the knowledge to identify, diagnose, and fix this common problem. Remember preventative maintenance is key to keeping your engine running strong. Now get out there and fix that issue!
Key Questions Answered: Bank 1 Air-fuel Ratio Imbalance
What are the common symptoms of a bank 1 air-fuel ratio imbalance?
Rough idling, misfires, hesitation during acceleration, poor fuel economy, and a check engine light are all potential indicators. Sometimes, the engine might feel like it’s struggling to run smoothly.
How do I test the air-fuel ratio sensors?
Using diagnostic tools and comparing sensor readings between banks is crucial. Proper testing methods and procedures, using the correct equipment, are important for accurate results.
What are some preventative measures to avoid bank 1 air-fuel ratio issues?
Regular maintenance, including fuel injector cleaning, air filter replacement, and ignition system checks, can prevent future problems. Keeping your engine healthy is a crucial part of prevention.
What are typical repair costs associated with fuel injectors?
Costs vary depending on the make and model of the vehicle and the specific components needed. A good estimate is crucial, so checking with a qualified mechanic is essential for accurate pricing.